Spill containment/absorbents
Does the color of an absorbent tell you anything about what it will safely absorb?
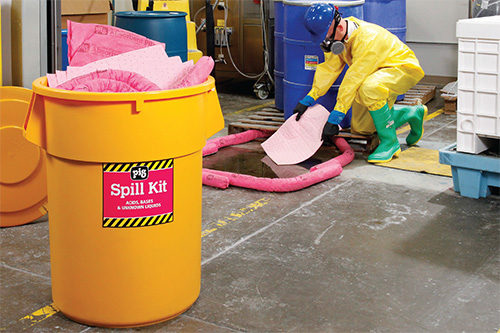
Responding is Karen D. Hamel, EHS specialist and technical writer, New Pig Corp., Tipton, PA.
Absorbents come in every color of the rainbow, and the color of an absorbent is often an indicator of what it will safely absorb. Even though no universal color standards apply to all brands of absorbents, there are similarities across brands.
For this discussion, the focus is on common absorbent products – not specialty items such as neutralizers. Absorbents are typically designed for one of the following three categories of liquids: oil and petroleum products, corrosive chemicals, and non-corrosive chemicals.
Absorbents for oil and petroleum products
Because oil and petroleum spills often happen outdoors, these absorbents are designed to repel and float on water while selectively absorbing the oil or petroleum product. Absorbents for oil products are most often white or brown. White absorbents allow the responder to see how much oil has been absorbed so they know when the product has reached full saturation and needs to be replaced. In a large-spill scenario, they also are a good visual indictor to anyone in the area that something is being done to correct a bad situation.
Brown absorbents also are designed to absorb oils and repel water. Most commonly, they are used for long-term deployment in areas such as retention ponds where the facility owner wants to have an absorbent product pre-deployed in case of a spill, without drawing unnecessary attention to the area.
Absorbents for corrosive chemicals
Using the wrong absorbent with corrosive liquids can cause unwanted heat reactions and other safety hazards. When working with corrosives, it is important to choose absorbent materials that will not react, such as polypropylene or earthen materials. Absorbents that contain cellulose will react with corrosive liquids.
Because extra caution is needed when corrosive liquids spill, absorbent manufacturers typically use bright colors such as pink, yellow and green to help draw attention to the fact that something has spilled and cleanup is underway.
Absorbents for non-corrosive chemicals
Absorbents used for everyday leaks and spills of products such as oil, coolants and solvents are commonly gray or blue. These colors are chosen because they blend into most industrial and manufacturing settings. This allows them to “quietly” do their job of absorbing leaks, drips and overspray all day without drawing attention.
Because chemical resistance is not a concern, cellulose and other lower-cost materials are often used to make absorbents for non-corrosive spills. Because these materials are less expensive than polypropylene, using these absorbents helps facilities to better manage costs while still providing a highly effective leak and spill control solution.
Training employees to choose the appropriate absorbent for the job helps to control costs because expensive absorbents that are needed for a spill of corrosives are less likely to be wasted cleaning up a water spill near the ice machine. It also helps ensure the safety and efficiency of anyone responding to a spill.
Editor's note: This article represents the independent views of the author and should not be construed as a National Safety Council endorsement.
Post a comment to this article
Safety+Health welcomes comments that promote respectful dialogue. Please stay on topic. Comments that contain personal attacks, profanity or abusive language – or those aggressively promoting products or services – will be removed. We reserve the right to determine which comments violate our comment policy. (Anonymous comments are welcome; merely skip the “name” field in the comment box. An email address is required but will not be included with your comment.)