OSHA fact sheet focuses on root cause analysis as part of incident investigation
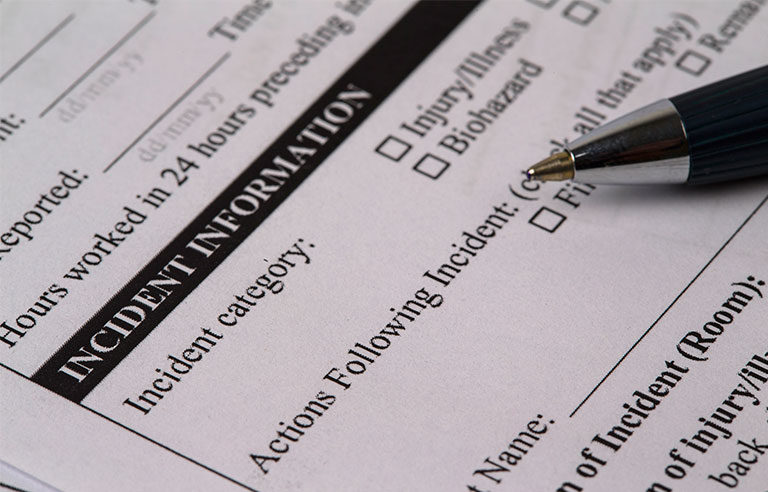
Photo: bdStudios/iStockphoto
Washington – OSHA and the Environmental Protection Association are urging employers to perform a root cause analysis after an incident or near miss occurs at a facility, in a recently released fact sheet.
The fact sheet defines a root cause analysis as a “fundamental, underlying, system-related reason why an incident occurred that identifies one or more correctable system failures.” Root cause analysis is important for any incident related to OSHA’s Process Safety Management Standard and EPA’s Risk Management Plan rule, the fact sheet states.
Fixing only an immediate cause of an incident or near miss may not correct the entire problem, the agencies caution. Brainstorming, checklists, logic/event trees, timelines, sequence diagrams and causal factor determination should be used in combination while conducting a root cause analysis to pinpoint what happened, how and why the incident or near miss occurred, and what needs to be fixed to ensure it does not happen again.
“Interviews and review of documents, such as maintenance logs, can be used to help answer these questions,” the resource states. “Involving employees in the root cause investigative process, and sharing the results of those investigations, will also go a long way toward preventing future similar incidents.”
Post a comment to this article
Safety+Health welcomes comments that promote respectful dialogue. Please stay on topic. Comments that contain personal attacks, profanity or abusive language – or those aggressively promoting products or services – will be removed. We reserve the right to determine which comments violate our comment policy. (Anonymous comments are welcome; merely skip the “name” field in the comment box. An email address is required but will not be included with your comment.)