Safety Leadership: The risks with routine
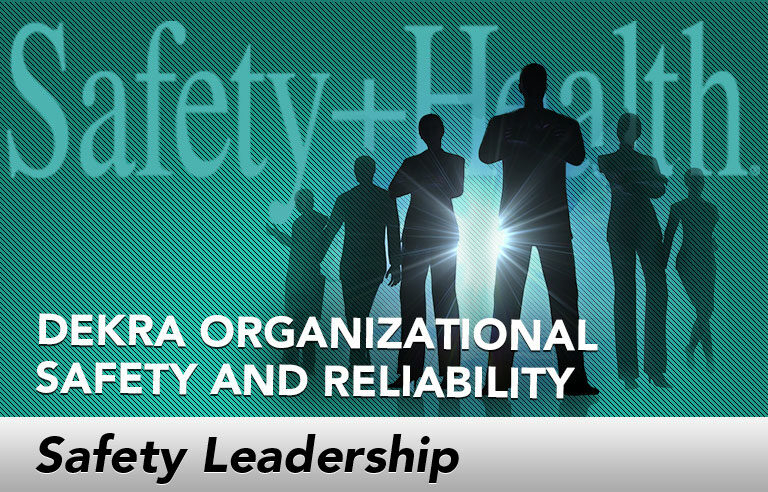
Editor’s Note: Achieving and sustaining an injury-free workplace demands strong leadership. In this monthly column, experts from global consulting firm DEKRA Insight share their point of view on what leaders need to know to guide their organizations to safety excellence.
In my job, I get the chance to visit with some of the world’s greatest minds on safety. One such person is Dr. Susan L. Koen. Koen is an expert on human reliability, workplace fatigue and high-performing work systems. In this Q&A, Koen, the CEO and founder of RoundtheClock Resources Inc., reveals why performing the same tasks time and time again can contribute to failing to recognize changes and the associated risks.
Jill Wiltfong: Much of our understanding about the risks of routine starts with research from the 1930s, correct?
Susan L. Koen: Yes, the first clues as to the inconsistency and fallibility of human performance were discovered in 1935, as pilots switched from one type of airplane to a more complex one. In concentrating on mastering the bells and whistles of the new plane, they had straight-up forgotten important procedures, leading to a series of crashes. Against this background, Boeing developed a checklist for pilots. It’s not the step-by-step checklist alone that produces performance reliability in aviation. Rather, it’s the recognition amongst pilots that they’re fallible. It’s the commitment to not operate from memory, because human memory is not reliable. And, most importantly, it’s the system of having two people cooperate in working through and cross-checking each critical task.
Wiltfong: Are checklists and cross-checking enough on their own?
Koen: Checklists are only one aspect of our workplaces among 19 that need to be adapted to the functioning of the human brain. Additionally, there are different levels – the organizational, team and personal levels. At the organizational level, leadership behaviors and corporate culture play a large role in preventing human error, because these elements set a tone, generate expectations and directly influence the individual performance of employees. Work instructions must be brain-aligned, taking into account the human vision system and how it best accesses and processes information. Also, teamwork often is undervalued in business, yet this level can function as an important bridge between the organizational and individual levels. Successful teams work well together and support their members.
Wiltfong: How should work instructions be formulated?
Koen: Work instructions should always be created from the perspective of the person who will be performing the job. The optimal solution is to involve the employees in the instructions’ creation, or have them create the instructions entirely. Presentation also plays a huge role – work instructions should be well laid out and accompanied by graphical representations or photographs to add clarity. If work instructions are not formatted appealingly, the human eye simply won’t process the information on the printed page or electronic display.
Wiltfong: Your research has demonstrated that we see things more with our brains than with our eyes.
Koen: That’s right. In one experiment, we investigated how we optically scan our environments. In an oil refinery, a sample needed to be taken and analyzed from an alkylation plant. In the pre-task briefing, attention was drawn to the specific dangers of taking that sample, as well as where employees should focus while doing so. In the briefing, the employees’ brains were conditioned, or “primed,” to pay attention to certain items in their work situation. The consequence, however, is that the brain becomes “blind” to other potential dangers, resulting in poor situational awareness. We have to understand this potential exposure and do more brain-aligned briefings.
Wiltfong: Is it possible that we also need to reconsider management styles?
Koen: It has been recognized at some management levels that companies must do more to lead people effectively. Sadly, many people still are in the dark when it comes to how leaders affect performance. When both sides have access to the same knowledge, they are better able to communicate with and adapt to one another, driving toward the same goal of human performance reliability. I have witnessed how companies are able to change for the better and achieve lasting gains in safety and reliability. So, I know that it’s possible.
This article represents the views of the author and should not be construed as a National Safety Council endorsement.
DEKRA Insight Organizational Psychologist Dr. Susan L. Koen is an expert on human reliability, high-performing work systems and workplace fatigue.
Jill Wiltfong is senior vice president of Business Innovation at DEKRA Insight and DEKRA Business Assurance.
Direct to your inbox: Sign up to be notified in email about new "Safety Leadership" columns.
Post a comment to this article
Safety+Health welcomes comments that promote respectful dialogue. Please stay on topic. Comments that contain personal attacks, profanity or abusive language – or those aggressively promoting products or services – will be removed. We reserve the right to determine which comments violate our comment policy. (Anonymous comments are welcome; merely skip the “name” field in the comment box. An email address is required but will not be included with your comment.)