Addressing changes in the utilities industry
How have the products used by utilities workers in recent years evolved to address changing demographics and working conditions?
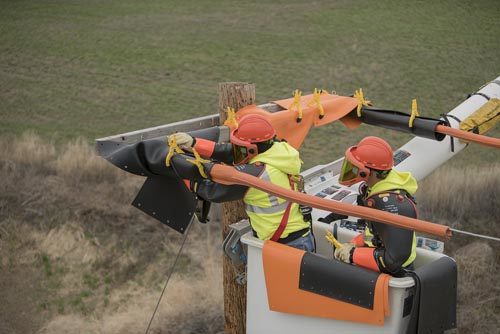
Responding is Richard A. Rivkin, president and CEO, Saf-T-Gard International Inc., Northbrook, IL.
Utility workers continue to face unique dangers. At any given moment, utility workers must deal with one or more occupational hazards, including low visibility, high-voltage contact, working at height, working in confined spaces, challenging weather conditions (rain and snow), work zone safety, and arc-flash risks. Exposure to these hazards undeniably increases workers’ likelihood of injury.
Although it may seem obvious that utility workers should be well aware of their need to use rubber-insulating equipment, an unnecessarily high amount of fatalities still occur because of contact with electrical equipment.
According to the Electrical Safety Foundation International, contact with overhead power lines was the largest fatal electrical accident category from 1992 to 2010, comprising 44 percent of all electrical fatalities. Many of these deaths could have been prevented had the workers used the appropriately tested and certified rubber-insulating equipment.
Rubber-insulating products such as gloves, blankets, sleeves, line hose and hoods used by electrical workers today are manufactured in accordance with industry consensus specifications under the auspices of ASTM International. However, rubber gloves are the only protective gear designed for constant contact with, and protection from, energized conductors and equipment. To be effective, rubber-insulating gloves must incorporate high dielectric and physical strength, along with comfort, flexibility and durability to increase the likelihood they will be used. Flexibility and proper fit are key.
Fortunately, both rubber-insulating gloves and leather protectors have improved dramatically in recent years to directly address these concerns, as well as others. Newer rubber formulations of insulating gloves offer increased flexibility and dexterity to minimize hand fatigue so linemen can wear them for an extended time without their hands cramping. This increased flexibility makes them ideal for working on high-voltage lines and equipment.
Furthermore, outdoor sun protection products are available in formulas that won’t harm the rubber, so linemen can protect themselves from both the sun and electrical hazards without worry.
Additionally, rubber-insulating gloves are being made in a wider range of sizes to accommodate even more workers. Typically manufactured in sizes 8 to 12, often in half sizes, some manufacturers also now offer rubber-insulating gloves as small as size 7 and as large as size 13. Proper fit will increase the likeliness that workers will wear the gloves, as gloves that are too big or bulky can affect tactile sensitivity, while gloves that are too small can cause discomfort.
In addition, equal care and consideration has been given to how leather protector gloves are made. Grain cowhide leather has been used more for its water-repellent properties, as linemen work in all types of weather. Moreover, additional grip enhancers can be added to various leather protector styles to deliver a wet or dry grip that won’t slip or affect the ergonomics of the gloves, even when working in the rain.
Editor's note: This article represents the independent views of the author and should not be construed as a National Safety Council endorsement.
Post a comment to this article
Safety+Health welcomes comments that promote respectful dialogue. Please stay on topic. Comments that contain personal attacks, profanity or abusive language – or those aggressively promoting products or services – will be removed. We reserve the right to determine which comments violate our comment policy. (Anonymous comments are welcome; merely skip the “name” field in the comment box. An email address is required but will not be included with your comment.)