CSB spotlights process unit startups, shutdowns in new ‘Safety Digest’
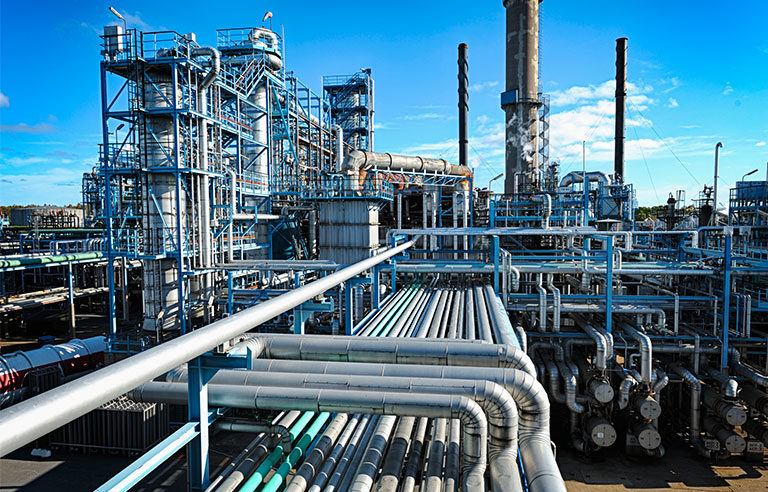
Washington — Effective process safety management can help prevent hazards and incidents related to process unit startups and shutdowns, according to a new Safety Digest from the Chemical Safety Board.
Process safety incidents are five times more likely to occur during startups than normal operations, the four-page document states, citing research from the Center for Chemical Process Safety. A 2010 study led by ExxonMobil showed that half of process safety incidents occur during startups, shutdowns and other infrequent events, likely because of non-routine procedures within the protocol.
The resource summarizes three CSB incident investigations – from 2001, 2002 and 2008, respectively – in which safety issues during startups or shutdowns led to a combined five fatalities and three injuries. In the 2001 incident, three workers at the BP Amoco Polymers plant in Augusta, GA, were killed when attempting to open a pressurized process vessel containing hot plastic. CSB found that inadequate process hazard analyses and process safety information contributed to the incident, which stemmed from an unsuccessful startup attempt 12 hours earlier.
The other incidents occurred at a First Chemical Corp. facility in Pascagoula, MS, and a Bayer CropScience plant in Institute, WV.
“To prevent these types of incidents from occurring, facilities should employ effective communication, provide workers with appropriate training, and have in place strong and up-to-date policies and procedures for hazardous operations such as startups and shutdowns,” the agency states.
Among CSB’s recommendations:
- Implement written operating procedures for startup after emergency shutdowns. Include sufficient detail and provide written checklists and diagrams to verify proper valve positioning, as needed.
- Conduct and complete a thorough pre-startup safety review. Do not bypass critical safety devices while troubleshooting startups and shutdowns.
- Ensure facility lockout/tagout programs require equipment to be rendered safe before opening for inspection or maintenance.
- Use proper procedures to isolate equipment after shutdowns.
- Inspect, calibrate and test computerized control systems.
Post a comment to this article
Safety+Health welcomes comments that promote respectful dialogue. Please stay on topic. Comments that contain personal attacks, profanity or abusive language – or those aggressively promoting products or services – will be removed. We reserve the right to determine which comments violate our comment policy. (Anonymous comments are welcome; merely skip the “name” field in the comment box. An email address is required but will not be included with your comment.)