The life span of respirator filters and cartridges
When should I change the filters on my half-mask respirator?
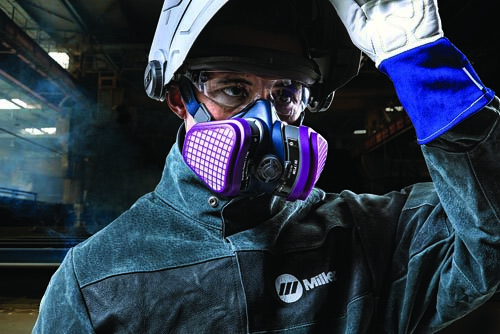
Responding is Emily Janssen, marketing specialist, welding accessories and cutting division, Miller Electric Mfg. LLC, Appleton, WI.
As outlined in OSHA’s Respiratory Protection Standard (1910.134), the importance of maintaining your respirator – including cleaning, disinfecting, inspecting and storing it – is key to keeping it functioning properly. This includes changing and maintaining filters and cartridges used in respirators. Filters and cartridges have a limited life span and are most effective when they are clean, unclogged and air is able to freely pass through them.
Filters
OSHA defines a “filter” as a component used in respirators to remove solids or liquid aerosols (e.g., particulates) from inhaled air. Under 42 CFR part 84, N, P or R designations are given to particulate filters. N series filters are used for any solid or non-oil-containing particulate, and R and P series filters are used for any particulate, including aerosols.
According to OSHA, the filter needs to be replaced when:
- The user has difficulty breathing comfortably or notices an increase of breathing resistance resulting from particle buildup.
- The filter becomes visibly dirty.
- The filter is physically damaged.
It’s important to note that N and R series filters may have limitations on use, as contaminants can degrade the filter media. Use limitations are outlined by the respirator manufacturer.
Cartridges
OSHA defines a “cartridge” as a container with a filter, sorbent or catalyst – or any combination of the three – that removes specific contaminants from air passed through the container. Cartridges must have an end-of-service-life indicator, which is typically indicated by changing colors.
Change-out schedule
In applications in which respirator use is mandated, OSHA requires employers to maintain a respirator cartridge change-out schedule as part of their written respirator program. (Consult the Respiratory Protection Standard for details.) The purpose of this schedule is to replace the cartridges before they reach the end of their service lives.
OSHA has three basic approaches to developing a change-out schedule: conduct experimental tests, use the manufacturer’s recommendations or use a math model. Each approach has its own advantages and disadvantages. For more in-depth explanations of these approaches and to help you choose the one that is appropriate for your application, go to osha.gov/SLTC/etools/respiratory/change_schedule.html.
Remember that safety and compliance are the most important considerations. OSHA recommends applying a “safety factor” to your change-out schedule to ensure the maximum life span of a cartridge is never exceeded.
It’s always better to replace filters and cartridges more often to ensure clean air flow for user comfort and compliance. For more information on a respiratory protection program, filters, cartridges and a change-out schedule, visit osha.gov/sites/default/files/2019-03/respiratoryprotection.pdf or osha.gov/video/respiratory_protection/maintenance_tran script.html.
Important: Always read and follow the manufacturer’s instructions and use limitations and all applicable ANSI, OSHA, CSA and other regulatory guidelines pertaining to the use of respirators. If you have questions about the respirator, consult your safety director and/or an industrial hygienist.
Editor's note: This article represents the independent views of the author and should not be construed as a National Safety Council endorsement.
Post a comment to this article
Safety+Health welcomes comments that promote respectful dialogue. Please stay on topic. Comments that contain personal attacks, profanity or abusive language – or those aggressively promoting products or services – will be removed. We reserve the right to determine which comments violate our comment policy. (Anonymous comments are welcome; merely skip the “name” field in the comment box. An email address is required but will not be included with your comment.)