Chemical Safety Board issues recommendations for preventing vapor discharges and fires
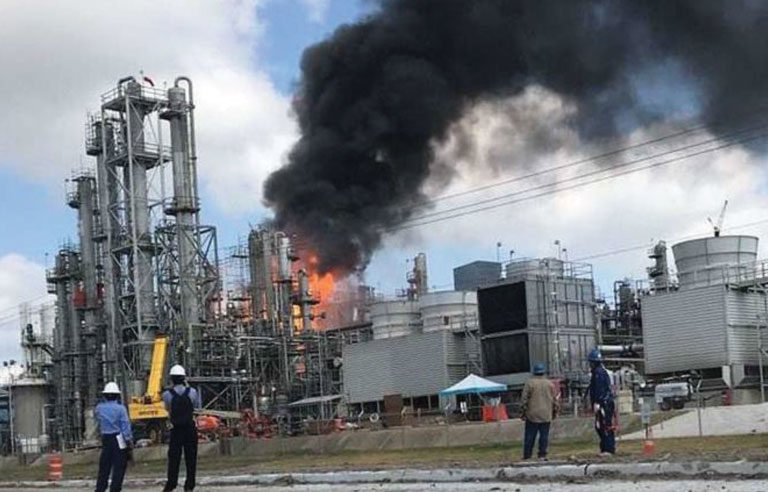
Photo: Chemical Safety Board
Washington — Discharge piping in chemical plants should be separate from areas that may contain workers, the Chemical Safety Board states in a final report on a May 2018 chemical release and fire at the Kuraray America Inc. plant in Pasadena, TX.
The recommendation, aimed at facility management, is one of 12. CSB found that high-pressure conditions developed in a plant reactor system after a scheduled maintenance shutdown. This activated the emergency pressure relief system, triggering a discharge of flammable ethylene vapor through piping and into a space where contractors were working.
More than 2,300 pounds of ethylene was released in about three minutes. The report states that welding being performed nearby likely caused the ignition. Twenty-three workers were injured, including some who jumped from second- or third-story structures to escape the fire.
In a press release, CSB Chair Steve Owens says the incident could have been prevented had plant officials ensured that discharge gas was routed to a safe location and evacuated the area at the sound of the reactor’s high-pressure alarm.
Sign up for Safety+Health's free monthly email newsletters and get the news that's important to you. |
In addition to facility design and the presence of nonessential workers during startup and upset conditions, the report identifies safety issues in several areas, including:
- Process hazard analysis safeguards. OSHA and Environmental Protection Agency regulations on process safety management govern safety programs that identify, evaluate and control hazardous chemicals. “Because these safeguards were ineffective,” high-pressure conditions inside the reactor reached emergency levels and prompted the vapor discharge.
- Process hazard analysis recommendations. “Safety recommendations stemming from a PHA must be resolved and documented.” CSB found that the facility didn’t act on a 2015 PHA recommendation related to possible ethylene discharge from emergency pressure relief systems.
- Operating procedures and training. A nightly breakdown of operating instructions provided by management conflicted with the company’s written operating procedures, CSB found. “Up-to-date written operating procedures that reflect current plant practices are necessary for the safe operation of a facility.” Further, the agency found that “critical gaps” in operator training contributed to the incident, and calls on the company to enhance its programs.
“The CSB’s final report and safety recommendations aim to take the valuable lessons learned from our investigations and implement necessary changes to improve workplace safety throughout this facility and across the country,” CSB member Sylvia Johnson said in the release.
Post a comment to this article
Safety+Health welcomes comments that promote respectful dialogue. Please stay on topic. Comments that contain personal attacks, profanity or abusive language – or those aggressively promoting products or services – will be removed. We reserve the right to determine which comments violate our comment policy. (Anonymous comments are welcome; merely skip the “name” field in the comment box. An email address is required but will not be included with your comment.)