Safe use of thermal fluids
How can effective health and safety protocols contribute to a safer and more effective work environment when thermal fluids are in use? What specific measures should be taken to prevent incidents?
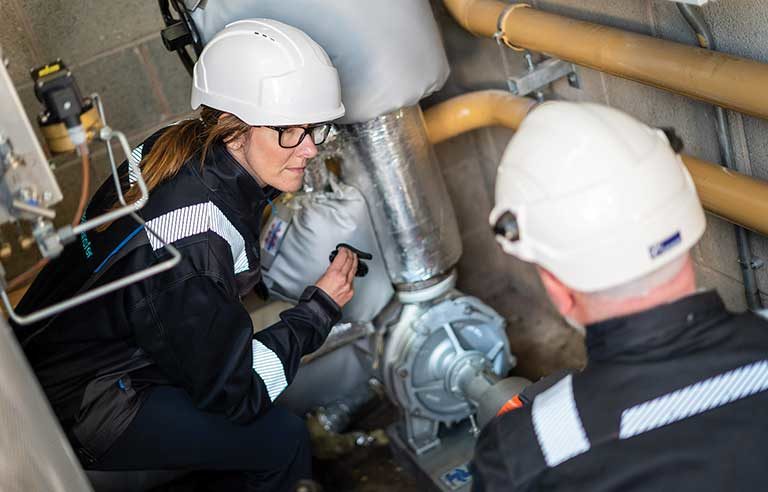
Photo: Global Heat Transfer
Responding is Tim Powell, thermal oil specialist, Global Heat Transfer, Staffordshire, England.
Manufacturers often use heat transfer systems to reach and maintain the high temperatures required for a variety of indirect heat transfer processes. Facilities traditionally invested in steam-based systems because water is affordable, seemingly sustainable and easy to source.
However, to reach the temperatures required in industrial processing, the system has to operate at very high pressures. If there was no way to effectively vent the steam, the pipes could burst.
Alternatively, thermal fluids can be designed for specific applications so they safely maintain temperatures at a lower rate of pressure for both heating and cooling applications, ranging from -130° F to 1,112° F. Heat transfer fluids are safer than steam and designed to provide years of effective use. Facilities that use them should still take proactive measures to extend fluid lifespan and ensure safety.
Managing risk
Heat transfer fluid will provide a great service for many years, but as it reaches the end of its lifespan, it will degrade, reducing thermal fluid efficiency and introducing by-products into the system. Relevant regulations stipulate how health and safety managers can reduce the likelihood of risks associated with degradation, but this is often easier said than done. This is because once thermal fluid enters the heat transfer system, it’s no longer visible, so any issues may go unnoticed until they affect production.
To effectively manage risk, health and safety managers should work closely with thermal fluid specialists to track fluid condition. Engineers should take a closed thermal fluid sample when the system is hot, live and circulating, using sampling equipment to provide an accurate representation of the fluid inside. Quarterly sampling and thermal fluid analysis enables engineers to outline its condition. Health and safety managers, alongside production and engineering managers, can use these results to track conditions over time and adapt procedures accordingly to reduce the risk of incidents caused by using degraded fluid.
Facilities can also invest in remote condition monitoring to further improve proactive maintenance, giving them real-time data that enables engineers to extend the safe and efficient use of thermal fluid for longer periods.
Maintaining the facility
While the engineers monitor fluid and system conditions to maintain uptime, health and safety managers can introduce protocols around the site to keep workers safe.
Encouraging good housekeeping not only aids productivity, it can also keep workers safe. Taking steps to clear pathways and remove electric cables, for example, are quick ways to remove trip hazards onsite. Health and safety managers should also place spill kits and personal protective equipment in close proximity to the system and ensure workers know where the equipment is so they can act quickly in case of an emergency. In addition, health and safety managers can commission thermal fluid experts to conduct site surveys and risk assessments to check the facility and recommend any areas for improvement.
When working with potentially dangerous and flammable substances, such as thermal fluid, health and safety managers should ensure teams pay close attention to any oil outside of the system, often caused by leaks or waste oil spills. Any spills should be cleaned up immediately – leaving them unattended can increase the risk of slips, trips and fires.
Introducing signage with information on safety procedures is key to regulatory compliance. Labeling flammable materials, high-voltage areas and other hazards are vital, while other signage can outline the best and safest procedures.
Training matters
Educating staff – both existing and new – on the importance of safety measures, as well as best practices for aspects such as thermal fluid monitoring, is integral to heat transfer maintenance.
Training the team on proactive maintenance ensures there’s always someone onsite who can effectively react to any issues immediately, keeping everyone in the facility safe.
Proactive measures – such as talking with thermal fluid specialists about regular fluid sampling, effective facility maintenance and comprehensive staff training – are essential for extending the lifespan of thermal fluid. By implementing these strategies, health and safety managers can mitigate potential hazards, ensure a safe working environment when working with thermal oils and help maintain compliance with local regulations.
Editor's note: This article represents the independent views of the author and should not be considered a National Safety Council endorsement.
Post a comment to this article
Safety+Health welcomes comments that promote respectful dialogue. Please stay on topic. Comments that contain personal attacks, profanity or abusive language – or those aggressively promoting products or services – will be removed. We reserve the right to determine which comments violate our comment policy. (Anonymous comments are welcome; merely skip the “name” field in the comment box. An email address is required but will not be included with your comment.)