NSC unveils SIF prevention model during Campbell Institute Forum

Orlando, FL — Amplify workers’ voices and keep learning, experts stressed Monday at the 2024 NSC Safety Congress & Expo during a Campbell Institute Forum discussion on serious incident and fatality prevention.
As panelists discussed the path to a new National Safety Council SIF prevention model unveiled during the presentation, they routinely returned to the importance of requesting and using feedback from the front lines.
“That’s where you get the benefit, when you hear from the people who do the job, the people who do the work, the people who understand the hazards – they’ve seen them,” said Christopher Petrouski, director of safety and security at U.S. Steel.
A vital part of the that, he added, is “not just hear, listen.”
Lori Guasta, senior director of consulting operations at NSC, noted the continuous research and discussion that helped shape the council’s SIF prevention model.
Although the model includes the familiar steps of the Plan-Do-Check-Act approach, it’s a streamlined version of a previous model – one with four steps instead of eight. And all while addressing the breadth of factors that influence SIF reduction in the industry.
The NSC model, Guasta noted, isn’t linear. It can be used regardless of organization size or industry. When customizing, she added, it’s important to keep SIF prevention under constant revision and remember that success depends on how SIF practices are applied during work.
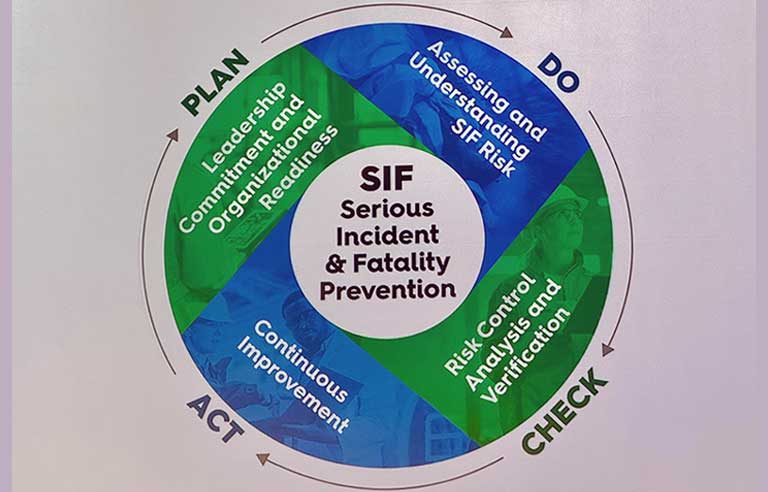
A closer look:
Plan: Leadership commitment and organizational readiness
Do: Assessing and understanding SIF risk
Check: Risk control analysis and verification
Act: Continuous improvement
“I’m proud to say this is a systems- and risk-based approach,” Guasta said. “There are four clear steps. You can’t control the risk if you don’t understand it.”
Guasta and Jeff Almond, chief thought leader at FailSafe, discussed how the occupational safety industry evolved its SIF prevention approach through the years. Initial models, for example, showed an effort to integrate principles of human and operational performance but were unclear about how to enact them.
Safety thought leaders progressed their research by harnessing the focus on various driving forces behind SIFs, including culture (employee engagement and value of safety, for example), management systems such as training and planning, process conditions, and human factors.
Guasta said the new model extends beyond an emphasis on SIF precursors while promoting continuous learning.
“To keep us curious, to keep us looking forward for improvement and enhancement,” she said.
Post a comment to this article
Safety+Health welcomes comments that promote respectful dialogue. Please stay on topic. Comments that contain personal attacks, profanity or abusive language – or those aggressively promoting products or services – will be removed. We reserve the right to determine which comments violate our comment policy. (Anonymous comments are welcome; merely skip the “name” field in the comment box. An email address is required but will not be included with your comment.)