Safety Leadership: For high reliability, start with the weak signals
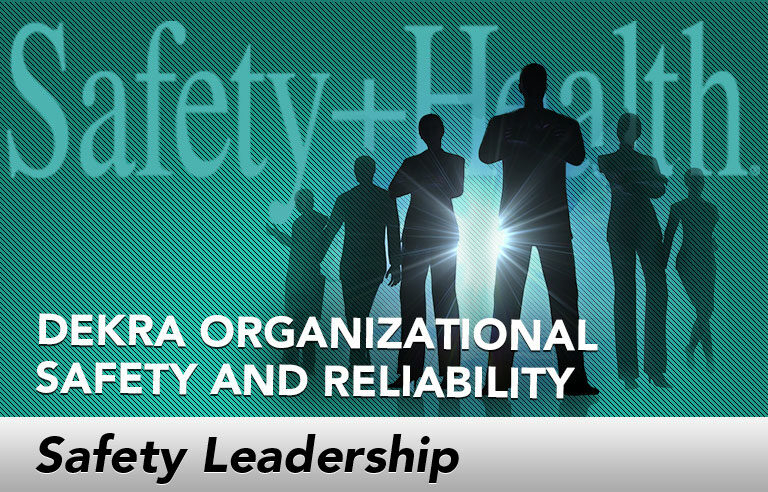
Editor’s Note: Achieving and sustaining an injury-free workplace demands strong leadership. In this monthly column, experts from global consulting firm DEKRA Insight share their point of view on what leaders need to know to guide their organizations to safety excellence.
Following a serious event, we often hear that it was a “disaster waiting to happen.” But the idea that the event in question was not just inevitable – but obviously so – oversimplifies a hard organizational reality: The signals of looming disaster aren’t always easy to detect. In real time, things like process deviations, unusual maintenance requests or even unexpected sounds coming from equipment seldom stand out against the hundreds of other data points, events, conversations and sensory inputs that leaders must process on a daily basis. Learning to detect those signals is the start of high-reliability performance.
Our study of catastrophic events identifies four distinct practices linked to high reliability:
- Anticipation – recognizing and acting on the weak signals that indicate potential for events
- Inquiry – countering cognitive bias by asking the right questions and diversifying perspectives
- Execution – using systems consistently and reliably
- Resilience – acting quickly to mitigate or minimize upset conditions
Of these, anticipation is foundational. Anticipation is the practice (some might also say art) of noticing – identifying and investigating the weak signals that could result in catastrophic events. Anticipation in practice means:
- People are encouraged to report and the value of reporting is reinforced.
- Information is captured from a variety of sources. Data is acted on (and people know it).
- Leaders understand and accept that there will be false positives.
Leaders can begin to cultivate an anticipation culture through their personal behaviors, which we call “Seek,” “Say” and “Reinforce”:
Seek. Leaders must seek out exposures, particularly those that are buried in routine work, reports or conversations. For many of us, day-to-day problems, variances or deviances are a nuisance that get in the way of productivity. But nuisance issues can actually be weak signals in disguise. Leaders must cultivate the patience not to hurry past the noise; a problem-seeking mindset views “quiet” periods with suspicion and looks at minor anomalies as potential harbingers of more significant problems in the system. Seeking behaviors include looking for exposure in both audits and inspections, as well as in works in progress.
Say. Often, in the wake of an incident, you’ll hear about people who “knew something wasn’t right” but didn’t feel comfortable raising their concerns. Leaders must develop a culture in which openly talking about what’s occurring – in the job and in safety – is accepted and practiced. Talking things out helps us think differently about a problem, and for others can foster understanding that helps us spot holes in our own thinking. In practice, this means openly stating your assumptions and hypotheses about anomalies you see in the data. It’s especially important to surface “sacrifice judgments” – those open or subconscious trade-offs made between production and efficiency goals and safety procedures. Asking employees questions about the work (e.g., How do you know this is working properly? What do you do if you have a problem?) can help them identify issues that need to be addressed.
Reinforce. In a high-anticipation culture, weak signals and anomalies surface regularly. Many of these issues will turn out to be minor or nothing. The far-thinking leader will continue to positively reinforce these “false positives,” knowing that each reinforcement is an investment in the reporting culture and will, at some unknown point in the future, result in uncovering a weak signal that truly is critical. Leaders serious about high-reliability performance must practice behaviors that make it safe for employees to raise concerns and demonstrate that all safety input is taken seriously. It is estimated that 10 percent of all mammograms result in a false positive, yet no one would dispute the value of further follow up in all cases. It’s the same in safety, where vigilance in attending to signals is critical to early intervention.
This article represents the views of the author and should not be construed as a National Safety Council endorsement.
Michael Mangan, Ph.D., is vice president of research and development for DEKRA Insight. His work helps organizations understand performance and design interventions for improvement.
Post a comment to this article
Safety+Health welcomes comments that promote respectful dialogue. Please stay on topic. Comments that contain personal attacks, profanity or abusive language – or those aggressively promoting products or services – will be removed. We reserve the right to determine which comments violate our comment policy. (Anonymous comments are welcome; merely skip the “name” field in the comment box. An email address is required but will not be included with your comment.)