The 2017 CEOs Who 'Get It'
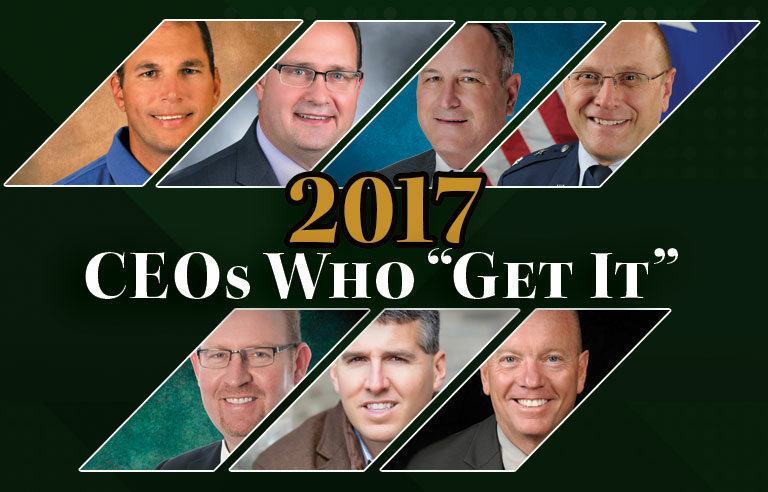

Larry Hogan
President
H+M Industrial EPC
Pasadena, TX
H+M Industrial EPC provides industrial design and design/build services to the chemical, petrochemical, and oil and gas industries. The company has serviced the Texas Gulf Coast for more than 25 years. H+M Industrial EPC employs 225 workers.
Why is safety a core value at your organization?
H+M Industrial EPC is committed to the goal of ensuring “continuous improvement” in all aspects of health, safety, and environment. In order to achieve this goal, the safety and health of all employees, contractors, customers, the environment and the public must receive primary consideration in the planning, scheduling and execution of work. Safety is a consistent part of how we do business. Our HSE culture is measured by our behaviors and actions, modeled by our leaders, and internalized by our team members. H+M implements several safety process elements to reduce risk to employees. All of the safety process elements are designed to work as a checks-and-balance system to ensure the closure of gaps that can occur while dealing with the diversity of the work scope, environment and human behavior. Integrating safety processes into all business functions and structures results in safety becoming embedded in the way an organization conducts business. By consistently measuring the effectiveness of our strategy, plans and standards, we will provide the foundation for continuous improvement.
Describe your personal journey to becoming a CEO who “gets it.” What experiences or lessons brought you to where you are now?
My personal journey to becoming a safety champion is continuously evolving every day. While I was formally trained in the engineering/design/construction profession, my knowledge of the safety profession was less extensive. This as a profession has grown on me, and I had to learn through my own observations and experiences throughout the years. In experiencing so many things and learning from many people over the 36 years I have worked in the industrial sector, I discovered a truth: Doing something safely requires much more than knowing the basics of how to do something – it requires a knowledge about the items and people encountered, a mindful attitude toward the task at hand, and vigilance of yourself and your surroundings that does not waver. Twenty-five years ago, it wasn’t uncommon for companies to go out and look at a job simply from a competitive cost-focused standpoint. Today, we do not bid on any job without considering if the job can be executed safely and our plan for ensuring it is executed safely.
What is the biggest obstacle to safety at your organization, and how do you work to overcome it?
Growth and the costs associated with it. It wasn’t long ago when H+M did not have a full-time HSE representative, much less a department of three to four safety professionals. It was a pretty big jump to go from a small budget to a budget that covered an entire department, including the equipment and supplies.
To overcome this initial shock, we had to change our mindset and come to terms as to what the real costs would be if someone gets hurt or we have multiple safety incidents because we did not provide the necessary funding to cover the safety budget.
Over the course of several years, we have successfully changed our culture by truly putting safety first.
We do understand that there are associated costs to work safely, but they are required regardless of what it takes, and the cost is so much greater if we allow our workers in the field to take on risks they should not be taking. As our business grew, our safety awareness grew, and we began to understand that striving to maintain a heathy and safe workforce was not only the right thing to do because we were good owners, it was also the economically smart thing to do. We must ensure we hold fast to what we learn. It is difficult to draft a cell phone policy or a policy dealing with a particular construction hazard. It is more difficult to hold true to those principles we believe in when “under the gun” to get a project done in adverse conditions or coaxed by our own conscience to let things slide a time or two. It is possible to get away with some things some of the time, but all unsafe things will carry a penalty at some point or another.
Every step is necessary and well worth the wait because I know that it is a step closer to making sure everyone goes home in one piece. What I do affects you, and what you do surely affects me.
How do you instill a sense of safety in employees on an ongoing basis?
At H+M, we promote a culture of safety awareness and employee engagement. Every employee has the authority to stop any job that might cause harm to themselves, the environment or the public. We all have a responsibility to take ownership of our personal safety as well as the shared responsibility of the safety of others. Safety is a team effort and we strive to expand safety awareness with a “brother’s keeper” attitude. I do my best to lead by example and keep my employees out of harm’s way. Everyone deserves to go home safe to his or her family at the end of the day and in one piece. We have implemented the TIP behavior-based safety process to identify and correct at-risk behaviors to aid in the prevention of accidents. Corporate office suggestions, supervisor suggestions and craft suggestions provide a three-cylinder approach to the identification and elimination of hazards throughout the company. Additionally, we have a safety incentive program that encourages individuals to become more engaged and positive toward safety. This program targets the workforce, who is most exposed to risks and is focused on proactive initiatives and behaviors and not on incidents. One of the incentive program elements recognizes a safety champion on a quarterly basis for their personal HSE commitment that empowers and embodies a positive HSE culture.
How does your organization measure safety? What are the leading indicators that show you how safe your organization is, and where do you see room for improvement?
Leading indicators will transform your safety culture from reactive to proactive by encouraging all levels of employees to actively participate in identifying and solving problems, reducing complacency and embodying the spirit of continuous improvement, and increasing overall safety awareness. The challenge is to engage your employees in a manner where they become empowered to complete and communicate a quality JSA or be an active participant in the company behavior-based safety process. The basics of hazard identification are a critical component to creating a safe workplace. Managing risk requires the understanding of potential hazards from design through construction. To ensure resources are available for targeted improvement, our leadership team critically reviews all HSE process elements. In order to assess these processes effectively, our whole leadership team conducts quarterly HSE field inspections in which the findings and recommendations are discussed at our monthly meetings. This hands-on involvement provides my team with the ability to make decisions (processes, procedures, initiatives, training needs, etc.) with a much more specific knowledge of how the job actually works and how it affects things on the front line.
What role does off-the-job safety play in your organization’s overall safety program? What types of off-the-job safety and health programs does your organization offer to employees?
Safety is a mindset that should be used at work, but should also be taken home with you, too. It is not a concept that expires or loses relevance through the ages. It does not lose strength (unless ignored or abused), and it is nearly transparent if integrated into our work programs. At H+M, we sponsor teams for various fun runs, participate in Texas Adopt-A-Beach cleanup and distribute “safety training alerts” that discuss various off-the-job safety tips (back to school, holiday, summer, etc.).
We also have several health and wellness initiatives to encourage our employees to take control of their health by rewarding healthy lifestyle choices with gift cards and reduced health insurance costs, among other company recognitions.
Post a comment to this article
Safety+Health welcomes comments that promote respectful dialogue. Please stay on topic. Comments that contain personal attacks, profanity or abusive language – or those aggressively promoting products or services – will be removed. We reserve the right to determine which comments violate our comment policy. (Anonymous comments are welcome; merely skip the “name” field in the comment box. An email address is required but will not be included with your comment.)