The 2017 CEOs Who 'Get It'
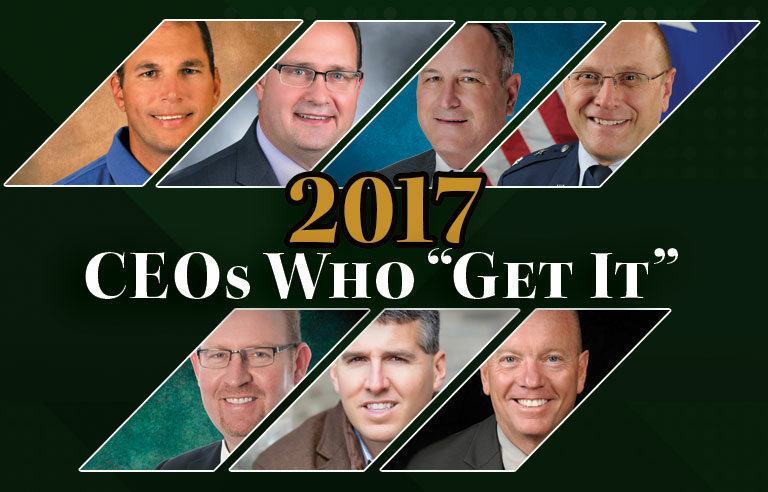

Tim Murray
CEO
Aluminium Bahrain B.S.C.
Askar, Kingdom of Bahrain
Aluminium Bahrain B.S.C. (Alba) is one of the leading aluminum smelters in the world. Alba produces more than 960,000 metric tons per annum of the highest-grade aluminum, with products such as standard and T-ingots, extrusion billets, rolling slab and molten aluminum. Alba employs approximately 2,700 people, a majority of which are nationals.
Why is safety a core value at your organization?
At Alba, we believe that a successful safety culture is linked to the financial performance of the company. A good and healthy safety culture impacts the lives of our employees and all other stakeholders of Alba. We want people to focus on safety in every part of their lives, and with that intention, we organize safety campaigns throughout the year. Our campaigns are based on Alba’s core safety values or ZERO Accident Principles:
- Ownership of safety is everyone’s responsibility.
- Working safely is a condition of employment.
- All work-related injuries and illnesses are preventable.
Ownership of safety comes from the heart and attaining zero injuries at the workplace is a journey that requires teamwork. The more support we receive from our people, the more we can embrace the changes and the more we make an impact on our lives. The targeted safety campaigns and messages have had a positive impact on safety and health at our workplace, which is evident from the reduced lost time injuries, as well as overall safety performance. This has been accomplished only through the extraordinary support of our employees in embracing the change of better safety and health environment.
Describe your personal journey to becoming a CEO who “gets it.”
Two months before I was appointed CEO, Alba had its fifth fatality in less than three years. It was a horrifying experience. Our safety performance was not good.
Safety was my biggest concern as the CEO. This was a big challenge to me because I came from a financial background. I had general experience in operations but none in safety specifically. I knew we had to start over with safety, as I refused to let the situation continue as it was.
I feel personally responsible for safety. For many years, we relied on a consultant to help manage our safety. I did not want a consultant’s view of safety. I wanted safety to be a daily core function of all our operations and thus, we took over the safety operations from the consultant.
You cannot outsource safety! You have to own it, you have to believe it. That is why our first safety principle, “Ownership of safety is everyone’s responsibility,” is the most important one. If and only if you believe in something will you do it.
We also introduced colors to our safety principles – white, yellow and pink, which got visual attention from our employees.
You can say we overhauled safety. The whole idea about safety is that it is about the people, our people … and not a PR exercise.
My aim is to have a Zero Accident Work Environment. I want our people to come to work safely, work safely, go home safely and be safe at home. You are here to work for your children, we want you to go home to your children. We don’t want you not to come back from work.
I would say that my No. 1 achievement as CEO is that we have had no fatalities while I’ve been CEO. By touching the heart, we can change the mind and that’s how I would think of safety. Seeing is believing!
What is the biggest obstacle to safety at your organization, and how do you work to overcome it?
Taking the ownership of safety also brings in risks … ones that I was willing to take on.
This is an industrial plant. It is tough . . . there is molten metal, there is heavy equipment moving around. What we do is dangerous and it will never get any easier.
Historically, the mindset here was more that of compliance; thus, shortcuts and poor safety behavior. It’s not just that you have the policies and procedures, you need to be aware.
The Arab culture is warm, welcoming and friendly. While it is excellent, people also tend to be very friendly and polite with safety issues. I tell people “On safety, it’s not okay to be polite. I want you to challenge any unsafe act. I would rather give a warning than a death certificate.”
The fundamental shift was to get people to believe because change starts with belief. We had to drive the ownership of safety to the shop floor. We decentralized safety; we brought in day-to-day safety coordinators allocated to every department of the plant. I spent two-thirds of my time on the shop floor, communicating directly with our people. It is easier to cut through the layers of communication with basic shop floor visits. They needed to see and feel that I believed in it.
In terms of contractors, we had to push big toward changing the safety attitude. I believe that the contractors, once in our plant, are our employees. So we involved them as well in everything we did.
Teamwork was and remains one of the key issues in achieving our ultimate objective of ZERO accidents. I shall quote Patrick Lencioni, “Remember teamwork begins by building trust. And the only way to do that is to overcome our need for invulnerability.”
And teamwork comes from trust. Trust is fundamental to safety culture; if your people do not trust you, then how anything can be achieved?
How do you instill a sense of safety in employees on an ongoing basis?
We want people to be proactive in terms of safety. That is the behavioral change that we intend to achieve.
Every new joiner has to undergo safety orientation. Safety induction and safety trainings are a part of our operational activities.
All the campaigns we do are a way to keep the momentum on safety. We also want to make safety fun – we come up with interesting ideas, for instance we had a blizzard campaign during summer. The themes and campaigns are very powerful to unite everyone under the idea.
Safety, when driven by the company’s management, sends out a strong message to all employees.
Visibility of the executives and senior management at work, especially the shop floor, is one of the main elements that we focus on. Safety campaigns involving executives and senior management helps to better convey messages. After all, seeing is believing.
We also push safety strongly during the summer months, especially during the holy month of Ramadan. Hot work environment combined with hot weather conditions and fasting: All these are dangerous conditions to work in. We take extra effort to support the workers during these challenging times, and conduct visits during various hours. While we may not be able to physically help the workers, we can surely help to boost their morale and ensure they work safely.
We also rely heavily on social media as a great tool for mass communication. Our PR team actively posts all our safety messages and campaigns on our own accounts on Instagram, Facebook, Twitter, etc. This helps to send our message across to employees who do not have email access, as well as tell the world out there what we do in here.
How does your organization measure safety? What are the leading indicators that show you how safe your organization is, and where do you see room for improvement?
We have in place typical reactive measures, such as number of fatalities, injuries and lost time injuries and accidents.
In terms of being proactive, we still have a long way to go. We have departmental key performance indicators where factors such as number of attendees for health and safety trainings, number of inspections performed, number of safety visits and interaction with the employees on the shop floor, behavioral observations captured into the e-Behavioral Observation system and number of near misses reported are measured.
One of the leading safety indicators for our organization is the near-miss reporting system. This allows us to identify incidents and happenings, which have a potential cause of injury or accident, and thereby implementing measures to mitigate the causes of the near miss.
We are currently improving on the near-miss reporting system to include a detailed follow-up on the near misses. We are also seeking to indulge more resources to work closely with the departments on the near misses.
What role does off-the-job safety play in your organization’s overall safety program? What types of off-the-job safety and health programs does your organization offer to employees?
With the company, we conduct post-working safety visits, visits during weekends or night shifts, and visits that are performed during special occasions such as Eid al-Fitr where most of our employees are available on-site.
Going beyond the gates of Alba, we actively educate the communities on safety matters of daily life through targeted campaigns such as the child booster seat campaign as well as impart safety trainings to our clients. As a leading organization in the Kingdom of Bahrain, we view this as one of our ways to give back to the society.
Moving away from the business, Alba takes a keen interest in hosting and sponsoring social and recreational activities such as industrial football and basketball leagues, reputed national annual horse races, golf tournaments and similar events held in the Kingdom. This sense of appreciation and gratitude toward the employees as productive members of the society is also evident in a number of employee-based social programs held during occasions such as the annual Ramadan Sports Season, Alba Family Day Festival and the Celebration of the National Day of the Kingdom of Bahrain.
Post a comment to this article
Safety+Health welcomes comments that promote respectful dialogue. Please stay on topic. Comments that contain personal attacks, profanity or abusive language – or those aggressively promoting products or services – will be removed. We reserve the right to determine which comments violate our comment policy. (Anonymous comments are welcome; merely skip the “name” field in the comment box. An email address is required but will not be included with your comment.)